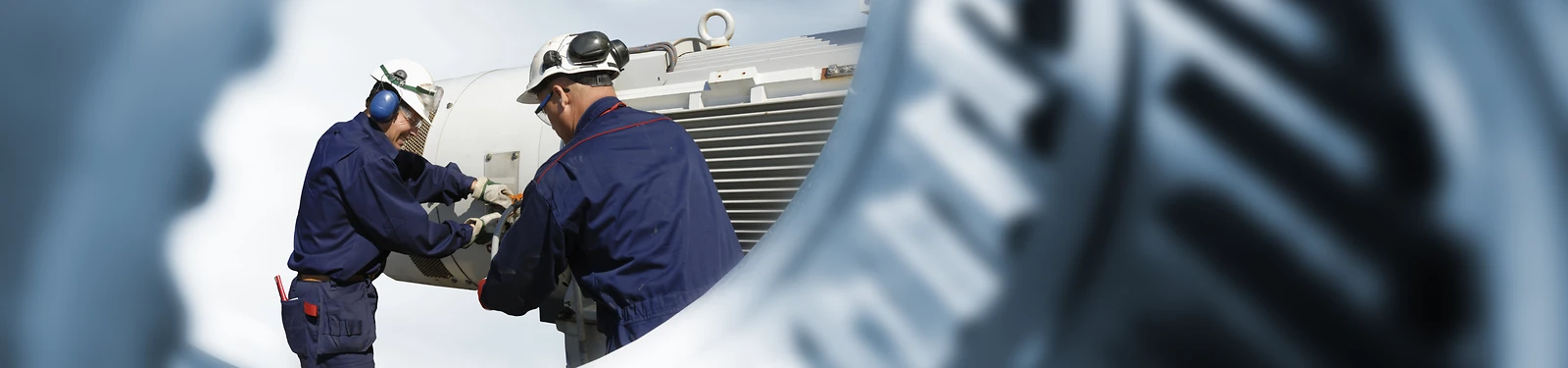

Lifecycle
The expertise and technology to help you operate safely and optimize performance.
From installation, calibration, startup, turnarounds, and aftermarket repair, PML has you covered.
We work to create value for you by delivering services that support all aspects of the equipment lifecycle to help you operate safely, consistently, and economically. Through collaboration, we aim to understand your objectives, determine where support is needed, and align deliverables to meet your needs to achieve consistent and repeatable results.
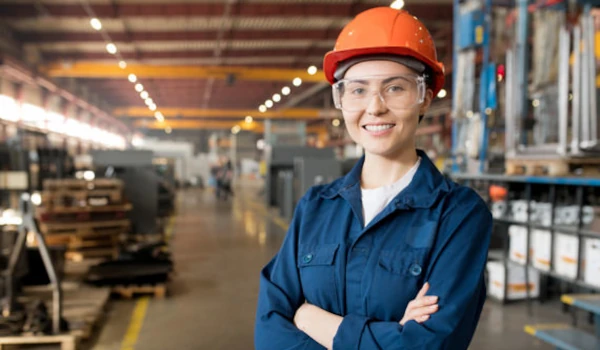
PORTFOLIO OF LIFECYCLE SERVICES
(click to expand)
Annual Cybersecurity Assessment
Secure your process control system from cybersecurity risks
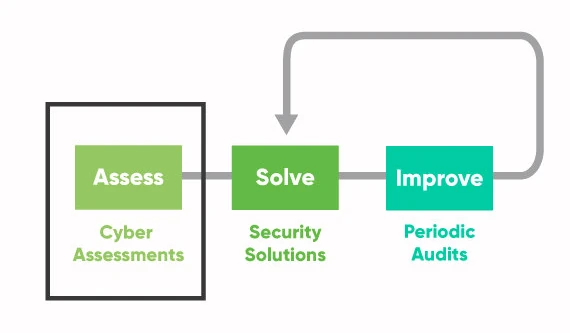
Every day, there are new headlines proclaiming the current global malware spreading is the “largest ever” and that, despite any protections employed, multimillion dollar cyber-criminal organizations are working very hard to get to our assets. The good news is that each new revelation makes us re-think whether our systems are fully protected from these attacks.
The consequences of a cyber-attack can cause serious damage to your plant, reduce, or shut down production, and even have safety and environmental implications. Use Emerson and PML’s Annual Cybersecurity Assessment service to identify vulnerabilities, and remediate protection gaps, and secure your process control system from cybersecurity risks.
Key Benefits
Our Annual Cybersecurity Assessment service will help you understand how secure your system is relative to best practices and provide guidance on how to make improvements. In addition, this service also identifies gaps in your control system security giving you the opportunity to remediate those weaknesses. With our help, you can strengthen your control system security protection and meet your system availability and operational integrity requirements.
The loss of revenue due to a cybersecurity attack can be extensive. Help prevent potential loss of revenue and brand reputation while reducing the risk of liabilities with our Annual Cybersecurity Assessment service.
Backup and Recovery
Backup and recovery service for peace of mind
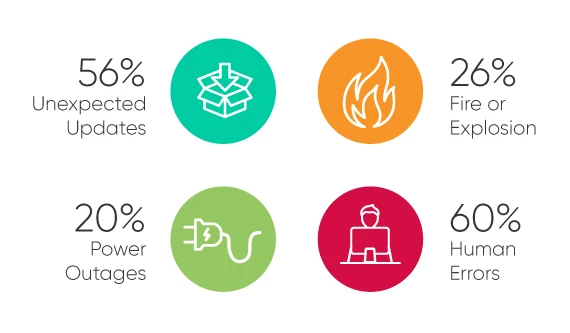
Your plant produces many things, including the data required to operate, manage and document your plant processes. How do you go about protecting this data and ensuring that a loss of data will not disrupt production?
The Consultation Process
1) Our field service engineers will work with you to determine what data needs to be backed up
2) We then work with your team to decide where to backup this data for disaster recovery purposes
3) A naming convention is developed with your team for the backed up data
4) We jointly determine the frequency of required backups
5) We determine the frequency required to perform periodic data verification tests of all backed up data to check for corruption, etc.
Commissioning & Start Up – Measurement
Ensure correct installation, commissioning and start-up
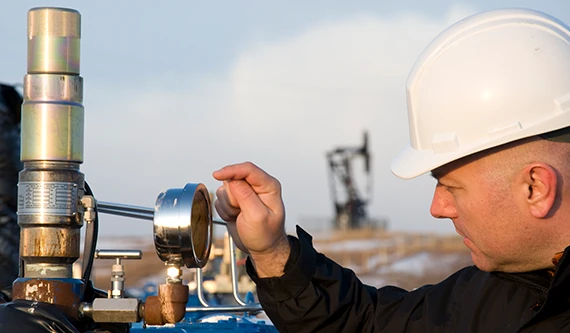
Specifying, selecting, and procuring an advanced measurement package is only part of the process. Tightening regulatory standards require the use of more complex measurement systems than ever before; correct installation, commissioning and start-up are vital.
The Highest Possible Measurement Accuracy
PML’s measurement commissioning and start-up support team can collaborate with your installation team to ensure the highest possible measurement accuracy. Once the advanced measurement package is installed, a field service technician will commission and start-up the package while training your field operations personnel for successful operation.
Control Valve Service and Repair
Fisher-certified repair
DeltaV Analyze Alarm Reports
Alarm performance and its impact on your operator effectiveness
DeltaV Analyze Alarm Reports make it easy to find the alarms that occur most frequently, are stale alarms, fleeting alarms, chattering alarms, alarms that experience long delays for operators to acknowledge and those that are most often suppressed. Proper Alarm Management implementation ensures that the correct alarms are annunciated to the operator at all times. This includes all modes of process operation.
Poorly configured alarms in the control system lead to millions of dollars of direct losses per year and even more in production losses. Alarm “floods” lead to unsafe conditions and increase the probability of incidents resulting in financial loss.
Financial Impact of Poor Alarm Management
Our reports can better identify gaps to help you to manage your alarm load, identify bad actor alarms, and help you meet regulatory compliance. By taking advantage of this service, you can obtain an assessment of your current alarm performance vs. industry standards, identify what DeltaV features are available to address problem areas, and implement the tools on your system.
DeltaV Lifecycle Consulting & Maintenance
With OEM factory-trained and certified specialists
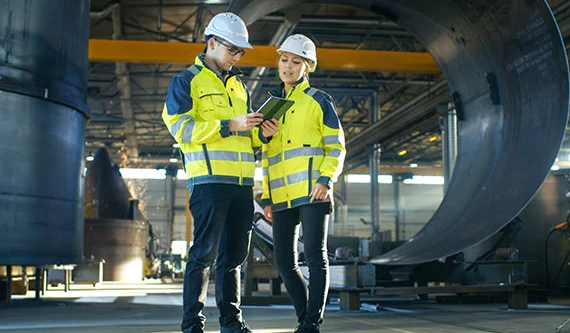
Emerson and PML have original equipment manufacturer (OEM) factory trained and certified field service specialists with the expertise and experience to help our customers maintain their DeltaV installations and offer the following lifecycle consulting and maintenance services:
DeltaV Loop
Know how well your control loops perform on your DeltaV System
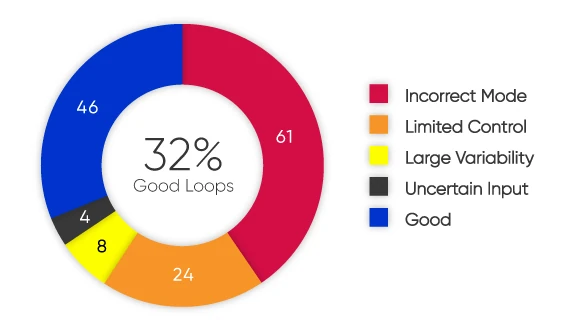
The Control Performance Score in the DeltaV Dashboard is intended to make you aware of control performance improvement opportunities to help improve plant operations by improving Safety, increasing Production, and lowering Costs. With DeltaV Loop Service, you will have additional resources at your disposal to help improve your Control Performance Score.
Highlights
Benefits
DeltaV System Health Management
Improve your DeltaV system’s availability and reduce your risks
System health management, defined here as the systematic elimination of risks to system reliability, security and performance, is an ongoing process. The system health score in DeltaV measures how well risks to your system’s safety, security and process are being managed. The fewer the number of open or unaddressed risks to your system, the better the score. Change is constant, and so is the need for an effective, sustained and measurable program of system health management.
Defined System Health Management Program Benefits
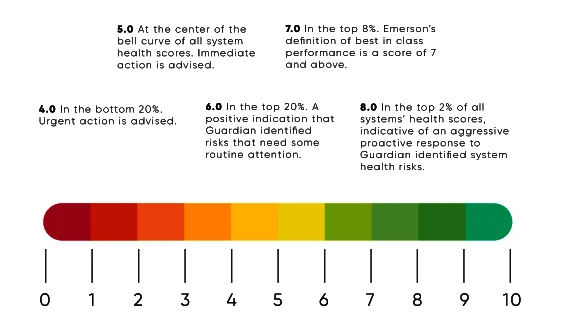
Interpret Your System Health Score
Gas Chromatography Maintenance
Ensure continuous and optimum performance
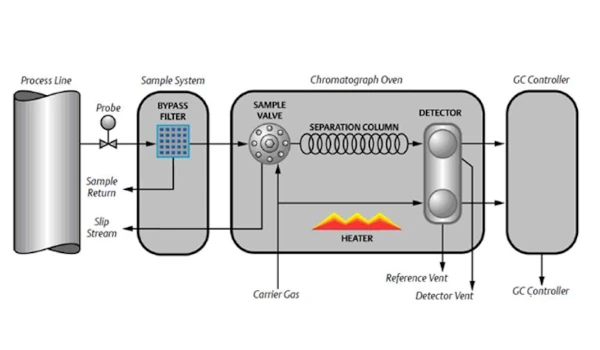
Regular service and calibration of gas chromatographs are key. PML provides important regular service and calibration of gas chromatographs.
Service Includes
Instrumentation Field Services
Complete field services for valve and instrument products
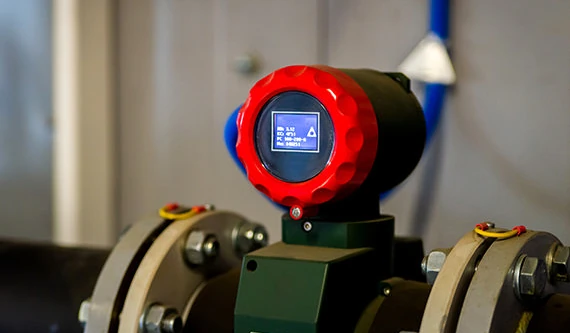
Automated valves and instruments are very sophisticated, intelligent devices comprised of sensitive electronics, complex materials and intricate designs.
This complexity coupled with a shortage of technical work force in the field increases the risk of improper installation and maintenance of your instrumentation assets.
We have a fully staffed team of technical specialists focused on specific product families to provide the best support necessary for the products we’ve supplied.
Instrumentation Calibration Services
Keep operations running efficiently, reliably, and safely
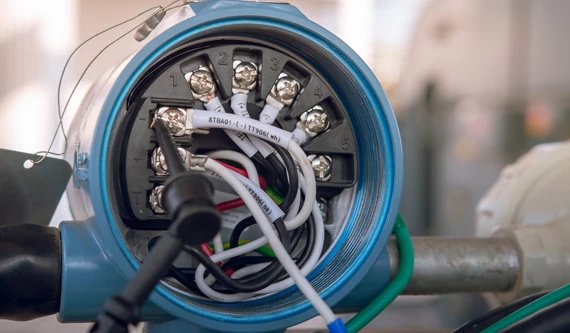
PML can help you keep your measurement instrumentation calibrated, configured and functioning.
Inaccurate process measurements can adversely impact your quality, reliability and profitability. Our local technicians are able to calibrate any type and model of measurement device to ensure your operations are running efficiently, reliably and safely. If scheduled calibration frequencies is a requirement in your industry, entrust the work to our service personnel to ensure it’s done properly – and promptly. This added support allows your maintenance staff to focus on other more important tasks.
Advanced Device Diagnostic Tools to Identify / Troubleshoot Instrumentation Issues Early
Safety and Pressure Relief Valve Testing & Repair
An authorized provider of Emerson pressure management products
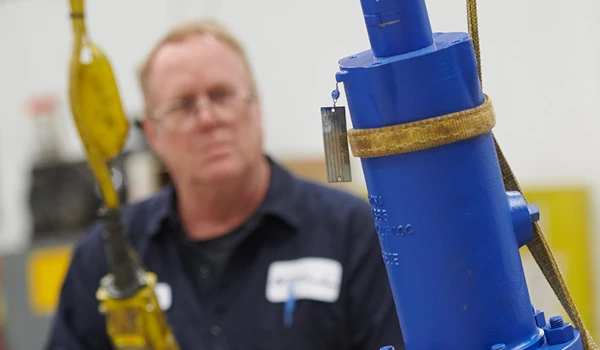
Our technical expertise and experience with valve repair, being an Emerson Authorized Service Repair Facility and a National Board of Boiler and Pressure Vessel Inspectors “VR” and T/O Certified Workshop would ensure that we provide quality end product and services without compromising the health and safety of personnel and the environment.
• Two (2) NBBI Approved J-Tube Test Benches to facilitate air, nitrogen and liquid test medium at 3,500 PSI
• One (1) Ventil test bench to test to facilitate air and liquid test medium at 4,350 PSI / 300 BAR
• In-house paint shop
Remote DeltaV Preventative System Maintenance
Preserve the DeltaV DCS system availability and reliability
Improve business performance and protect your automation investment with one of the largest global services and support organizations in the industry.
Emerson factory trained and certified service specialists will perform a prescribed set of maintenance tasks using a standard and proven procedure. This expertise is supported by more than 40 years of process systems industry experience and thousands of customers worldwide. DeltaV Scheduled System Maintenance and Preventive Maintenance provides site services to proactively maintain and continually advance and enhance your Emerson control system installation.
With this program, you can keep your control system hardware and software maintenance requirements up-to-date while maintaining a flexible path forward to new technology.
Benefits
The execution of this service can be done remotely by enabling a cybersecure remote connection between PML and the customer’s ProPlus station following all Emerson cybersecurity guidelines. This will allow our service engineer to run the data collection and Analysis tools to capture the system health parameters used for analysis. In case this remote connection is not available, our office can provide instructions to the customer about how to access and execute the standard tools.
Site Evaluation
Achieve maximum operational performance and reliability from DeltaV DCS
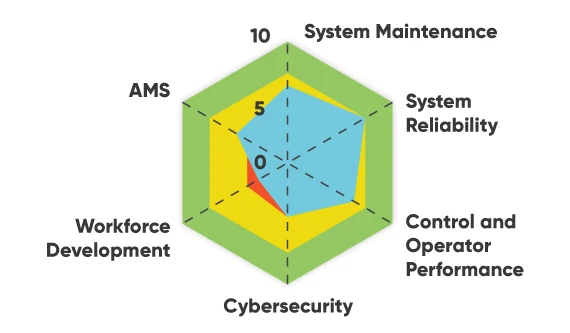
An innovative, proactive evaluation process to get the maximum operational performance and reliability from the DeltaV distributed control system (DCS).
The Site Evaluation Service will enable customers to assess the configuration state and performance of the main elements of their system against Emerson’s best practices, determining areas for improved performance and highlighting potential issues to process performance and uptime.