

Asset Reliability
Keep assets available and producing with detection or diagnostics for conclusive insight.
Let’s improve your plant’s reliability and maximize the performance potential of all your production assets.
As industrial facilities have become more complex, so has the role of asset management. PML has the expertise to help your facilities move to a proactive and predictive approach for asset reliability. The introduction of new technology and services go a long way towards streamlining management. We ensure sustainable results and benefits are captured that are incremental to existing initiatives.
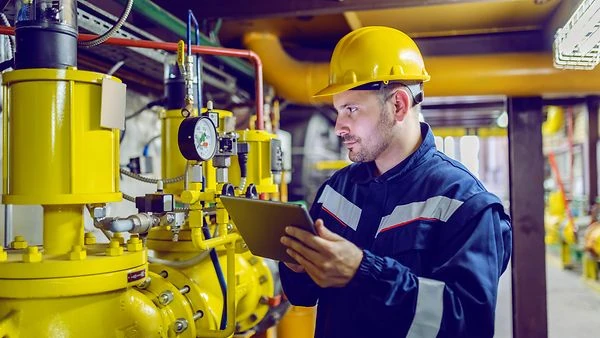
PORTFOLIO OF Asset Reliability Solutions
(click to expand)
Vibration Analysis
Let’s diagnose the source of plant vibration issues
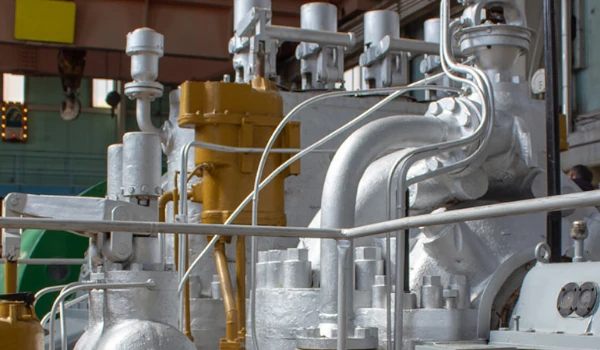
Vibration Analysis is critical in accurately diagnosing Rotating Equipment issues and identifying its root causes. Our team is highly trained, certified and with a wealth of experience working in the upstream Oil & gas, LNG, Petrochemical, Utilities and Manufacturing industries conducting vibration data collection and analysis of critical Turbo-machinery and Balance of Plant Equipment. We’ve assisted customers from the commissioning of their rotating equipment, implementation, and optimization of their vibration programs.
Motor Current Signature Analysis (MCSA)
The workhorse that drives pumps, gearboxes, fans, and more
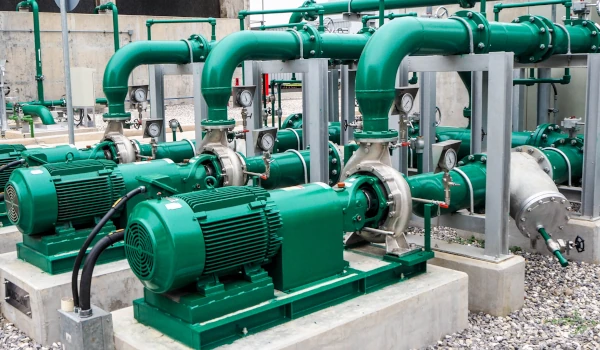
The AC Induction Motor is considered the workhorse in industry used in driving Pumps, Fans, Compressors etc. to achieve desired production rates. Motor Current Signature Analysis is a Condition Monitoring Technology used to accurately confirm the presence of suspected Rotor Bar Issues within the AC induction motor. This is accomplished by capturing motor current readings from the MCC Panel, after which it’s analyzed in the Frequency Domain. This is also very effective in diagnosing Mechanical Issues (Belts, Bearings, Gears, etc.) from the load being driven by the AC induction motor. Our team have been successful in conducting motor current signature analysis testing on 480 Volts and 4160 Volts motors, accurately diagnosing broken rotor issues after vibration was conducted. This accurate diagnostic greatly assisted our customers in the proper planning and scheduling of corrective actions resulting in minimal equipment downtime and impact to their production.
Resonance Detection
A critical tool to ensure safe and reliable operations
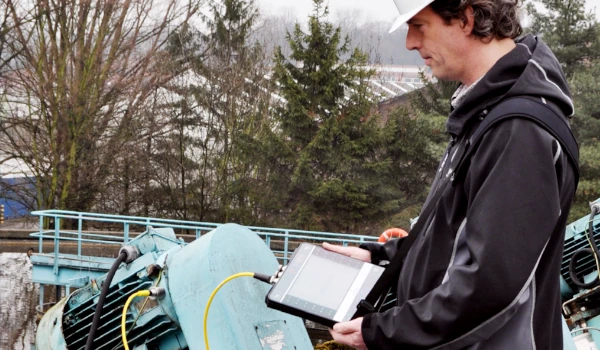
Resonance is a very destructive vibration force which can result in premature failures of rotating equipment bearings, mechanical seals, structures, and piping resulting in the loss of process containment which can result in fire or explosion. Resonance occurs when a system’s Natural Frequency coincides with any of a machines operating frequencies or piping excitations. PML offers advanced testing services such Bump Testing to accurately identify a system’s Natural Frequency. Other services include Coast Down / Run-Up checks on Turbomachinery to accurately identify the Critical Speeds of the Rotors to avoid any Resonance Issues during operation. These advanced testing and diagnostic capabilities provide customers with the accurate information required to perform Stiffening or Modifications of machine structures, Piping Supports and Operating Speeds of machines to avoid any Resonance Issues.
Transient Analysis
Facilitate asset optimization in a network
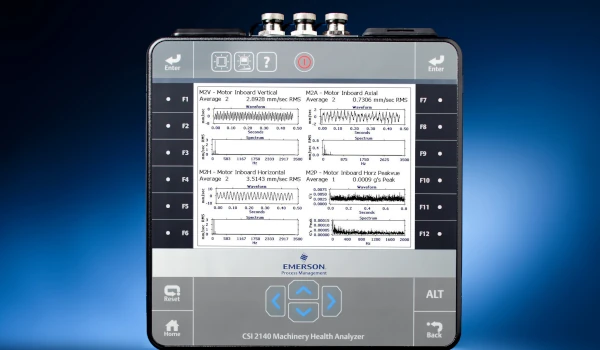
Routine vibration data collection during steady state operations of rotating equipment and piping systems might not reveal any vibration issues or abnormalities. Transient Analysis is a powerful technology used by PML to accurately identify the source of abnormalities that may occur during a process upset condition that can be missed during routine vibration data collection. PML can perform from single up to twenty-four (24) channels of continuous transient vibration data and other operating conditions on rotating equipment and turbomachinery to accurately diagnose the root cause of machinery problems.
Cross Channel Analysis
Detect faults to verify issues on machines
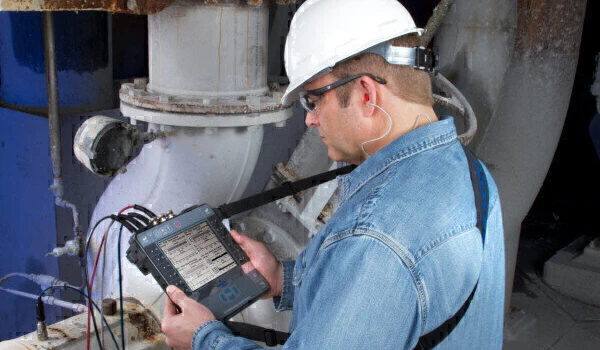
PML can employ the use of more advanced testing techniques such as Cross Channel Analysis. Some of these techniques include Cross Channel Phase, Impact / Modal Testing and Frequency Response Function (FRF) Analysis. Cross Channel Phase can be used to confirm the presence of the following defects in rotating equipment: Unbalance, Misalignment, Bent Shaft, Soft Foot, Structural Looseness. The other Cross Channel Analysis techniques can be used to determine the Mode Shapes, Stiffness and Damping of equipment, piping and structures.
Strobe-light Inspections
An effective tool for inspection and quality control
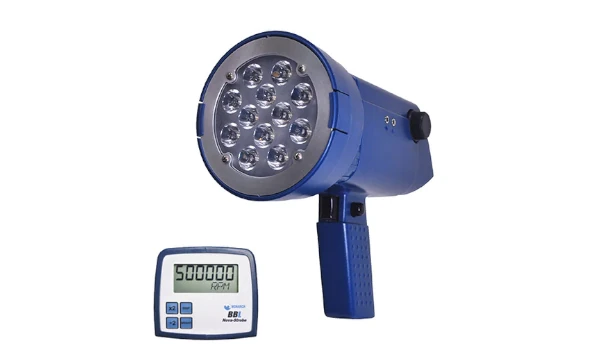
A simple but very powerful and effective technique used for conducting visual inspections of Couplings, Belts, Pulleys, Fin Fans and Motor Cooling Fans. This technique employs the use of an LED strobe-light that when tuned to the operating speed of rotating equipment, it flashes at the same this same rate causing a visual “Stop-Motion” effect so further inspections can be conducted on the rotating components. This is used to determine the presence of the following: